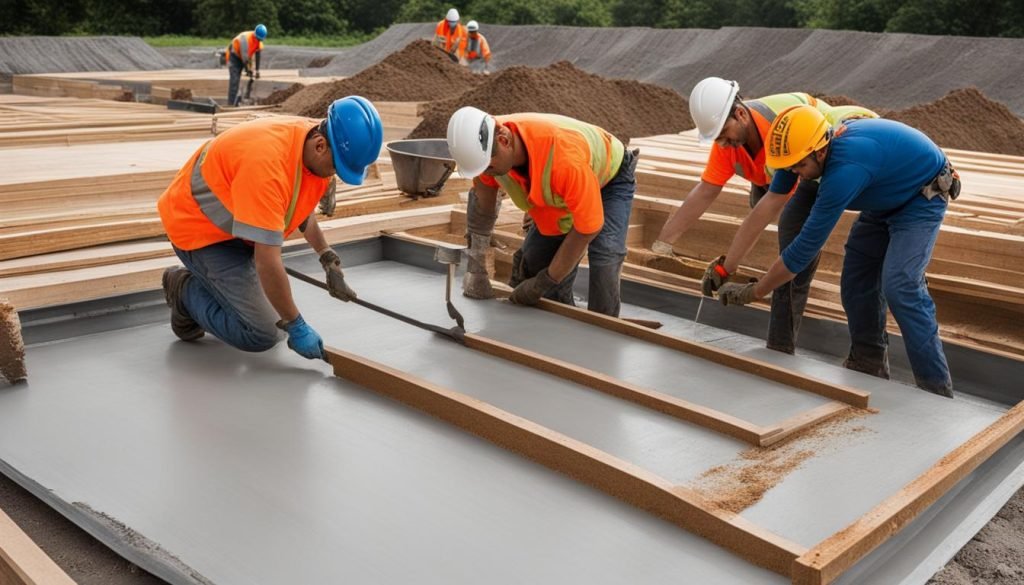
Engineered formwork is an integral part of concrete slab construction. It serves as a mold made of steel or aluminum that shapes the concrete structure. Once the concrete has hardened and cured, the formwork can be removed. However, the timing for formwork removal is crucial to ensure the strength, integrity, and durability of the concrete slab. Additionally, for individuals considering the enhancement of their space, Townsville Concrete Perfection informative guide on ‘How to Smooth Exposed Aggregate Concrete: Techniques and Tips’ offers expert insights.
The exact timing for formwork removal depends on various factors, including the type of cement, climate conditions, admixtures used, and the size of the forms and structure. Removing the formwork too soon can result in cracks and structural issues in the concrete, while delaying the removal unnecessarily can lead to project delays and increased costs.
Key Takeaways:
- Formwork removal should be done at the appropriate timing to ensure the strength and durability of the concrete slab.
- Factors like the type of cement, climate, admixtures, and structure size impact the timing for formwork removal.
- Removing formwork too soon can cause cracks and structural issues in the concrete.
- Delaying formwork removal unnecessarily can result in project delays and increased costs.
- Consulting with a site engineer and following recommended guidelines is crucial for successful formwork removal.
Factors Affecting Formwork Removal
The timing for formwork removal is influenced by several factors that play a crucial role in the safety and effectiveness of the construction process. Considerations such as concrete strength, temperature, type of cement, and formwork stability contribute to determining the appropriate time for formwork removal.
Concrete strength is a key factor in the decision-making process for formwork removal. The grade of concrete used and the type of cement employed significantly impact the time required for the concrete to achieve the necessary strength. The higher the concrete strength, the earlier the formwork can be removed, ensuring the stability and structural integrity of the construction.
The temperature at which the concrete is cured also affects its strength development. Higher temperatures accelerate the curing process, leading to faster concrete strength gain. Conversely, lower temperatures prolong the curing time, requiring more patience before formwork removal can be considered.
The stability of the formwork itself is vital when it comes to removing it safely. Formwork stability ensures that the structure remains intact during the removal process, minimizing any potential risks or damage. Stability can be achieved through proper construction techniques, the use of quality materials, and regular inspections to track the formwork’s condition throughout the curing period.
To estimate the concrete’s strength before removing the formwork, conducting tests on concrete cubes or cylinders is advisable. These tests provide quantitative data that helps in determining the concrete’s strength and informs the decision-making process regarding formwork removal.
By considering the concrete strength, temperature, type of cement, and formwork stability, construction professionals can ensure timely and appropriate formwork removal. Proper consideration of these factors not only guarantees the safety and integrity of the structure but also contributes to the overall success of the construction project.
General Guidelines for Formwork Removal
Properly removing formwork from a concrete slab is crucial to ensure the structural integrity and durability of the construction. The curing process plays a significant role in determining when formwork can be safely removed. Following the guidelines set by the American Concrete Institute (ACI) and considering the specific curing process are essential steps for successful formwork removal.
Curing Process
During the curing process, it is important to monitor the moisture and temperature within the formwork. Adequate curing allows the concrete to gain sufficient strength and durability. The specific time required for formwork removal can vary depending on several factors, including the type of cement used, environmental conditions, and the size and complexity of the structure.
“Proper curing is essential to achieve the desired concrete strength and prevent cracks and other defects.”
The American Concrete Institute provides general recommendations for the formwork removal timeline based on the type of cement used. It is generally suggested to wait 7 days for ASTM C 150 Type I cement, 10 days for ASTM C 150 Type II cement, 3 days for ASTM C 150 Type III cement, and 14 days for ASTM C 150 Type IV or V cement. However, these timelines may vary, and it is always best to consult with the site engineer for accurate recommendations.
Ordinary Portland Cement
For Ordinary Portland Cement, which is commonly used in construction, the timelines for formwork removal are typically shorter. Walls and columns can usually have their formwork removed after 24-48 hours, slabs after 3-4 days, and soffits after 1 week.
It’s important to note that these guidelines are general recommendations, and the specific formwork removal timeline should be determined in consultation with the site engineer. The engineer will consider factors such as the project requirements, concrete mix design, and environmental conditions to provide the most appropriate and safe timeline for formwork removal.
Summary
Formwork removal is a critical step in concrete slab construction. Adhering to the curing guidelines established by the American Concrete Institute and consulting with the site engineer ensures that the concrete has gained sufficient strength and durability before removing the formwork. Proper formwork removal contributes to a well-constructed and long-lasting concrete structure.
Formwork Removal Calculation
Proper formwork removal is crucial for successful concrete slab construction. Calculating the optimal time for formwork removal involves various factors, including determining the concrete strength and safe striking times. These calculations ensure the structural integrity of the concrete and prevent any potential damage that may occur during the removal process.
One method used for formwork removal calculation is based on the characteristic strength of concrete cubes or cylinders. These test specimens should have a similar maturity to the structure at the time of formwork removal. By comparing the strength of the test specimens to the desired concrete strength, the appropriate time for formwork removal can be determined.
In addition to test specimens, non-destructive tests on the structural member can also be conducted to evaluate the concrete strength. These tests provide valuable insights into the maturity and development of the concrete, allowing for a more accurate assessment of when the formwork can be safely removed.
The size of the concrete member, the grade and type of cement used, and the temperature during the curing process also play a significant role in determining the gain of concrete strength. These factors must be taken into account when calculating the formwork removal time.
Suggested Formwork Removal Times
Concrete Structure Type | Suggested Formwork Removal Time (Days) |
---|---|
Walls | 3-7 |
Columns | 3-7 |
Slabs | 7-14 |
Beams | 7-14 |
The table above provides suggested formwork removal times for different types of concrete structures. These times serve as general guidelines, and it is essential to consult with the site engineer to determine the specific formwork removal time for each project.
By accurately calculating the formwork removal time, construction professionals can ensure the safety and structural integrity of the concrete slab, preventing any potential issues that may arise from premature formwork removal.
Formwork Removal Specifications
When it comes to removing formwork from a concrete slab, following the proper specifications is crucial to ensure the structural integrity of the project. It is important to consider the importance of engineer supervision and take necessary precautions to prevent surface damage. Here are some key guidelines to follow:
1. Sufficient Concrete Strength
Before removing the formwork, it is essential to ensure that the concrete has developed sufficient strength to support its weight. This will vary depending on factors such as the type of cement, curing time, and environmental conditions. The engineer should assess the concrete’s strength and determine the appropriate time for formwork removal.
2. Arrange Formwork and Connections for Easy Removal
Proper arrangement of the formwork and connections is crucial to facilitate easy removal without causing damage to the concrete or formwork panels. The engineer should ensure that the formwork is securely attached and that there are no obstructions or interferences that can hinder the removal process.
3. Engineer Supervision
Engineer supervision is of utmost importance during the formwork removal process. The engineer should be present to oversee the entire procedure, ensuring the quality of the hardened concrete and minimizing any casting defects. Their expertise will help identify any potential issues and ensure that the removal is carried out safely and efficiently.
4. Wooden Wedges for Separating Forms
When separating the forms, the use of wooden wedges is recommended. These wedges allow for controlled and gradual separation, reducing the risk of sudden shifts or damage to the concrete. Care should be taken to avoid excessive force or improper angles when inserting the wedges.
5. Proper Sequence for Removing Props
Removing props should be done in the correct sequence to maintain the structural stability of the concrete slab. The engineer should provide guidelines on the appropriate order for prop removal, ensuring that the load is evenly distributed and that there are no sudden shifts that could lead to damage or collapse.
By following these formwork removal specifications, you can minimize the risk of surface damage, maintain the structural integrity of the concrete slab, and ensure a successful construction project.
Lay Out the Project
Before starting the concrete slab construction, it is crucial to properly lay out the project area. This involves careful consideration of factors such as drainage and space for forms. The following steps outline the process for laying out the project:
1. Prepare the Area
Start by preparing the area where the concrete slab will be constructed. This involves removing any topsoil to create a level surface. Ensure that the ground is adequately leveled and free from any debris or vegetation.
2. Level the Ground
Next, it’s essential to level the ground to ensure a stable and even surface for the concrete slab. Use a leveling tool to distribute the soil evenly and create a flat foundation. Fill any low spots with excess soil to achieve a uniform level across the project area.
3. Build Strong Forms
Strong and sturdy forms are crucial for supporting the concrete during the construction process. Use high-quality planks and heavy stakes to build durable forms that can withstand the weight of the concrete. Ensure that the forms are securely placed and aligned properly to maintain the desired shape of the slab.
4. Pitch the Surface
Proper drainage is essential to prevent water accumulation on the concrete slab. To achieve this, pitch the surface slightly by sloping it away from any nearby structures or areas prone to water pooling. This will ensure that rainwater or other sources of moisture drain away from the slab.
After following these steps, thoroughly soak the area and the forms before pouring the concrete. This will help prevent excessive absorption of water from the fresh concrete, ensuring proper curing and strength development.
Preparing for the Concrete Truck
Before the concrete truck arrives, it is crucial to make the necessary preparations to ensure a smooth and efficient process. Proper planning and attention to detail can help avoid delays and potential damage to your property.
Ensuring Access
One of the first steps in preparing for the concrete truck is to ensure that there is easy and safe access for the truck to reach the construction area. Consider any obstacles or potential hazards such as dry wells or weak spots that the truck may encounter. Clear the path and remove any obstructions to ensure a clear and safe route for the truck to enter the site.
Protecting the Lawn or Driveway
If the concrete truck needs to pass over the lawn or driveway, it is essential to take measures to protect these surfaces from damage. Place planks or boards along the path that the truck will take to provide a sturdy and protective surface. This will help distribute the weight of the truck and prevent it from causing any damage to your lawn or driveway.
Ensuring Formwork Width
If the concrete truck needs to drive between the forms, it is important to ensure that the forms are wide enough to accommodate the truck. Adequate space between the forms will allow the truck to maneuver easily and minimize the risk of damage to the forms or the truck itself. Take the necessary measurements and adjust the formwork if needed prior to the arrival of the concrete truck.
By taking these steps to prepare for the concrete truck’s arrival, you can ensure a smooth and efficient process. Careful planning and attention to detail will help protect your property and prevent any unnecessary delays or obstacles during the concrete pouring process.
Placing and Compacting the Concrete
When it comes to concrete construction, proper placement and compaction are crucial for achieving a durable and high-quality result. Whether you are using a concrete truck or a deep tray contractor’s wheelbarrow, it’s essential to follow best practices to avoid issues like segregation and contamination.
Start by using shovels to thoroughly compact the concrete. This ensures uniformity and strength throughout the structure. Avoid moving more concrete than can be comfortably wheeled in the barrow to prevent injuries and maintain control over the placement process.
Once the concrete is placed, it’s important to screed it using a timber section. This process helps level the surface and bring mortar to the top, creating a smooth and even finish. After screeding, float the surface to agitate it slightly and remove any excess mortar. This step enhances the surface’s quality and improves its resistance to wear and tear.
Benefits of Proper Compaction:
- Increased Durability: Thoroughly compacted concrete has improved resistance to cracking and structural damage.
- Better Strength: Proper compaction ensures the concrete reaches its maximum potential for load-bearing capacity.
- Reduced Segregation: By compacting the concrete uniformly, you can avoid the separation of aggregates and cement paste, which can weaken the structure.
- Minimized Contamination: Effective compaction prevents the intrusion of foreign materials or debris into the concrete, maintaining its quality and purity.
Remember, surface finishing should only be done once the concrete has hardened enough to avoid damage. Taking the time to place and compact the concrete properly will contribute to the long-term durability and performance of your construction project.
Contraction Joints and Surface Curing
When it comes to concrete slab construction, two critical aspects that require attention are contraction joints and surface curing. These play a vital role in preventing cracks and ensuring the durability of the concrete.
Contraction Joints
Contraction joints are essential because they create planes of weakness in the concrete. These joints help relieve the stress caused by shrinkage, which occurs as the concrete cures and dries. By strategically placing and cutting the contraction joints, the risk of cracks forming due to shrinkage can be significantly minimized.
To ensure effective contraction joint placement, these joints should be spaced no more than 2 meters apart. Additionally, it is crucial to cut the joints deeply into the concrete to allow for sufficient movement and stress relief.
Surface Curing
Curing the concrete’s surface is equally important in preventing cracks and maintaining its strength. Proper curing involves retaining moisture in the concrete for an adequate period, typically at least seven days. This moisture retention is crucial as it allows the concrete to continue hydrating and gain strength.
To extend the drying time and promote optimal curing, insulation can be employed. Covering the concrete surface with hessian or plastic sheets helps retain moisture and create the necessary environment for the curing process. By extending the drying time, the concrete has more time to fully hydrate, reducing the risk of cracks and ensuring its long-term durability.
It is essential to follow proper curing techniques, as recommended by industry experts, to achieve the best results. By paying attention to contraction joints and surface curing, concrete slabs can be constructed to resist cracking and maintain their integrity for years to come.
Benefits of Contraction Joints and Surface Curing | Prevention of Cracks | Extended Drying Time |
---|---|---|
Creates planes of weakness | Reduces stress from shrinkage | Allows for proper hydration |
Minimizes crack formation | Maintains concrete strength | Enhances long-term durability |
Improves structural integrity | Ensures surface integrity | Prevents premature drying |
Removing the Formwork and Clean-up
Once the concrete has gained enough strength to support its weight, usually after seven days, the formwork can be safely removed. Care must be taken to avoid using metal tools that can damage the concrete surface during the formwork removal process. Using wooden wedges for separation will prevent any surface damage.
Proper cleaning of tools used during the concrete construction is crucial for future use. Removing any hardened concrete and debris will ensure the longevity and effectiveness of the tools. Thoroughly clean all tools with water and a stiff brush, paying special attention to removing any cement or concrete residue.
It is important to protect the newly exposed concrete surface from rain or cold weather to prevent any potential damage. Covering the concrete with hessian or plastic sheets will shield it from adverse weather conditions, including rain or extreme temperatures.
Conclusion
Proper timing and techniques for removing formwork from a concrete slab are crucial for constructing a robust and durable structure. Various factors, including the type of cement, climate conditions, and the size of the structure, play a significant role in determining when formwork can be safely removed. By adhering to established guidelines and considering factors such as concrete strength and formwork stability, successful formwork removal can be achieved.
Following best practices during the concrete slab construction process, such as ensuring proper curing and surface finishing, is essential for achieving optimal results. By carefully monitoring the curing process, maintaining the right moisture levels, and providing adequate time for concrete to gain strength, the risk of cracks and structural issues can be minimized. Additionally, employing proper surface finishing techniques helps protect the concrete slab from damage and ensures a smooth and durable surface.
To ensure a well-constructed and long-lasting concrete slab, it is crucial to prioritize safety and take necessary precautions. Supervision by a qualified engineer is vital during the formwork removal process, as they can ensure the quality of the hardened concrete and identify any potential casting defects. Proper tools and techniques should be used when removing the formwork to prevent damage to the concrete surface, and the structure should be protected from adverse weather conditions to maintain its integrity.
FAQ
When should formwork be removed from a concrete slab?
The formwork should be removed once the concrete has hardened and cured sufficiently. The exact timing for formwork removal depends on various factors such as the type of cement, climate, and size of the structure.
What factors affect the timing for formwork removal?
Factors such as concrete strength, temperature, type of cement used, and formwork stability influence the timing for formwork removal. These factors must be considered to ensure the concrete has developed sufficient strength before removing the formwork.
Are there general guidelines for formwork removal?
Yes, the American Concrete Institute recommends waiting 7 days for ASTM C 150 Type I cement, 10 days for ASTM C 150 Type II cement, 3 days for ASTM C 150 Type III cement, and 14 days for ASTM C 150 Type IV or V cement. However, these are general guidelines and it is important to consult with the site engineer for the specific timeline.
How can formwork removal be calculated?
Formwork striking times can be calculated based on the characteristic strength of concrete cubes or cylinders with similar maturity to the structure at the time of formwork removal. Non-destructive tests and tables with suggested formwork removal times for different structural members can also be used to determine the strength of the concrete and the safe formwork removal time.
What are the specifications for formwork removal?
Formwork removal should be supervised by an engineer to ensure the quality of the hardened concrete and the prevention of casting defects. Separation of forms should be done using wooden wedges, and props should be removed in the correct sequence to maintain structural stability. Care should be taken to avoid damage to the concrete surface during formwork removal.
How should the project area be prepared before concrete slab construction?
The project area should be properly laid out, considering factors like drainage and space for forms. The topsoil should be removed and the ground leveled. Excess soil can be used to fill low spots. Strong forms should be built using planks and heavy stakes, and the area and forms should be thoroughly soaked before pouring concrete.
How can I prepare for the arrival of the concrete truck?
Ensure there is proper access for the concrete truck, considering any dry wells or weak spots that the truck may pass over. Use planks to protect the lawn or driveway if needed. If the truck needs to pass between the forms, ensure the forms are wide enough to accommodate the truck. Being prepared for the truck’s arrival will save time and money.
What is the best way to place and compact the concrete?
The concrete can be placed using a concrete truck or a deep tray contractor’s wheelbarrow. Thoroughly compact the concrete using shovels, avoiding segregation and ensuring proper compaction. Only move as much concrete as can be comfortably wheeled in the barrow to prevent injuries. After placing the concrete, screed it using a timber section and float the surface to agitate the concrete and bring mortar to the surface.
What are contraction joints and how should the concrete be cured?
Contraction joints are important to provide planes of weakness and prevent cracks in the concrete due to shrinkage. These joints should be spaced no more than 2m apart and cut deeply. Curing the concrete is essential to prevent cracking and maintain its strength. Moisture should be retained in the concrete for at least seven days, and insulation with hessian or plastic sheets can help extend the drying time.
How should the formwork be removed and what clean-up is required?
The formwork should only be removed once the concrete has gained enough strength to support its weight, typically after seven days. Avoid using metal tools that can damage the concrete surface. Properly clean all tools used during the concrete construction. If there is a risk of rain or cold weather, cover the concrete with hessian or plastic sheets to protect it.
Source Links
- https://theconstructor.org/building/formwork-removal-time-specification/11083/
- https://www.holcim.com.au/products-and-services/tools-faqs-and-resources/do-it-yourself-diy/home-handymans-step-by-step-guide-to-laying-concrete
- https://www.eiffeltrading.com/blog/post/how-long-should-you-wait-to-remove-concrete-formwork